Polylactic Acid Surgery
Poly(lactic acid) or polylactide (PLA) is a thermoplastic aliphatic polyester derived from renewable resources, such as corn starch (in the United States), tapioca products (roots, chips or starch mostly in Asia) or sugarcanes (in the rest of world). It can biodegrade under certain conditions, such as the presence of oxygen, and is difficult to recycle.
The name "polylactic acid" is to be used with caution, not complying to standard nomenclatures (such as IUPAC) and potentially leading to ambiguity (PLA is not a polyacid (polyelectrolyte), but rather a polyester)
Catalytic and thermolytic ring-opening polymerization of lactide (left) to polylactide (right)Bacterial fermentation is used to produce lactic acid from corn starch or cane sugar. However, lactic acid cannot be directly polymerized to a useful product, because each polymerization reaction generates one molecule of water, the presence of which degrades the forming polymer chain to the point that only very low molecular weights are observed. Instead, two lactic acid molecules undergo a single esterfication and then catalytically cyclized to make a cyclic dilactate ester. Although dimerization also generates water, it can be separated prior to polymerization due to a significant drop in polarity. PLA of high molecular weight is produced from the dilactate ester by ring-opening polymerization using most commonly a stannous octoate[citation needed] catalyst, but for laboratory demonstrations tin(II) chloride is often employed. This mechanism does not generate additional water, and hence, a wide range of molecular weights is accessible.
Polymerization of a racemic mixture of L- and D-lactides usually leads to the synthesis of poly-DL-lactide (PDLLA) which is amorphous. Use of stereospecific catalysts can lead to heterotactic PLA which has been found to show crystallinity. The degree of crystallinity, and hence many important properties, is largely controlled by the ratio of D to L enantiomers used, and to a lesser extent on the type of catalyst used
PLA has similar mechanical properties to PETE polymer, but has a significantly lower maximum continuous use temperature.
Polylactic acid can be processed like most thermoplastics into fiber (for example using conventional melt spinning processes) and film. The melting temperature of PLLA can be increased 40-50 °C and its heat deflection temperature can be increased from approximately 60°C to up to 190 °C by physically blending the polymer with PDLA (poly-D-lactide). PDLA and PLLA form a highly regular stereocomplex with increased crystallinity. The temperature stability is maximised when a 50:50 blend is used, but even at lower concentrations of 3-10% of PDLA, there is still a substantial improvement. In the latter case, PDLA acts as a nucleating agent, thereby increasing the crystallization rate. Biodegradation of PDLA is slower than for PLA due to the higher crystallinity of PDLA. PDLA has the useful property of being optically transparent.
PLA is currently used in a number of biomedical applications, such as sutures, stents, dialysis media and drug delivery devices. The total degradation time of PLA is a few years. It is also being evaluated as a material for tissue engineering.
Because it is biodegradable, it can also be employed in the preparation of bioplastic, useful for producing loose-fill packaging, compost bags, food packaging, and disposable tableware. In the form of fibers and non-woven textiles, PLA also has many potential uses, for example as upholstery, disposable garments, awnings, feminine hygiene products, and diapers.
PLA has been used as the hydrophobic block of amphiphilic synthetic block copolymers used to form the vesicle membrane of polymersomes.
PLA is a sustainable alternative to petrochemical-derived products, since the lactides from which it is ultimately produced can be derived from the fermentation of agricultural by-products such as corn starch or other carbohydrate-rich substances like maize, sugar or wheat.
PLA is more expensive than many petroleum-derived commodity plastics, but its price has been falling as production increases. The demand for corn is growing, both due to the use of corn for bioethanol and for corn-dependent commodities, including PLA.
PLA has also been developed in the United Kingdom to serve as sandwich packaging.
PLA has also been used in France to serve as the binder in Isonat Nat’isol, a hemp fiber building insulation.
PLA is used for biodegradable and compostable disposable cups for cold beverages, the lining in cups for hot beverages, deli containers and clamshells for food packaging.
The pharmaceutical industry uses oligolactic acid (OLA - a shorter polymer of lactic acid) in pressurized metered dose inhalers (pMDIs) as a surfactant. Studies have shown that on standing, pMDIs without OLA will yield a much higher dose than intended as compared to those containing OLA which delivers a fairly constant dosage
Other companies involved in PLA manufacturing are PURAC Biomaterials (The Netherlands) and several Chinese manufacturers. The primary producer of PDLLA is PURAC, a wholly owned subsidiary of [CSM] located in the Netherlands.
Galactic and Total Petrochemicals operate a joint-venture, Futerro, that is developing a second generation of polylactic acid product. This project includes the building of a PLA pilot plant of 1500 tonnes/year in Belgium.
The Korean research center KAIST has announced that they have found a way to produce PLA using bio-engineered Escherichia coli.
Since 2009, Purac has developed a unique business model by starting production of Lactides (D and L, the monomers for PLA production, in their Spanish production plant with a capacity of several thousands of tons, while in March 2010 the construction has started of a 75.000 tons lactide plant at their production site in Thailand (Rayong Province). Purac has developed the technology to polymerize these lactides with Sulzer, a Swiss Engineering company. Purac collaborates with various PLA production partners to develop production scale and new markets for PLA. Thanks to the availability of D-lactide, Purac partners will be able to use stereo-complex technologies to produce new PLA grades with heat-stability (HDT) up to 180 degrees C, enabling use in higher value application area's. In a tripartite collaboration between Purac, Sulzer and Synbra solutions were developed to allow Synbra to start production of PLA and subsequently E-PLA, an attractive biodegradable and/or biobased alternative to EPS-foam in avariety of application areas. This collaboration was awarded by Frost and Sullivan with the Innovation of the Year Award in 2008 citing "This unique offering will significantly reduce the process and product development time enabling faster and more reliable market entry for PLA producers".
Prior to injection, your plastic surgeon will add sterile water to reconstitute the polylactic acid. Then it's injected into the deep dermis or subcutaneous space with a special technique called tunneling or threading. It is important to distribute polylactic acid evenly to minimize the possibility of inflammatory formations called granulomas.
You will likely need about three monthly treatments to achieve your desired results. With each treatment, there is re-stimulation of your own collagen. Then it can take four to six weeks to see the full effect. While this type of dermal filler is considered semi-permanent, you may still need occasional touch-ups.
The only FDA-approved brand is Sculptra Aesthetic.
Visit the online referral service of the American Society of Plastic Surgeons (ASPS). ASPS, founded in 1931, is the largest plastic surgery organization in the world and the foremost authority on cosmetic and reconstructive plastic surgery. All ASPS physician members are certified by the American Board of Plastic Surgery (ABPS) or the Royal College of Physicians and Surgeons of Canada.

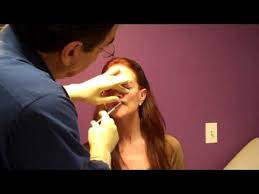

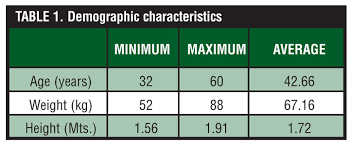


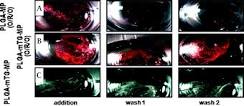
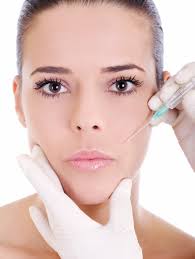

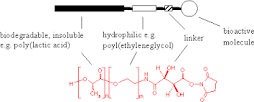


The name "polylactic acid" is to be used with caution, not complying to standard nomenclatures (such as IUPAC) and potentially leading to ambiguity (PLA is not a polyacid (polyelectrolyte), but rather a polyester)
Synthesis


Polymerization of a racemic mixture of L- and D-lactides usually leads to the synthesis of poly-DL-lactide (PDLLA) which is amorphous. Use of stereospecific catalysts can lead to heterotactic PLA which has been found to show crystallinity. The degree of crystallinity, and hence many important properties, is largely controlled by the ratio of D to L enantiomers used, and to a lesser extent on the type of catalyst used
Chemical and physical properties
Due to the chiral nature of lactic acid, several distinct forms of polylactide exist: poly-L-lactide (PLLA) is the product resulting from polymerization of L,L-lactide (also known as L-lactide). PLLA has a crystallinity of around 37%, a glass transition temperature between 60-65 °C, a melting temperature between 173-178 °C and a tensile modulus between 2.7-16 GPaPLA has similar mechanical properties to PETE polymer, but has a significantly lower maximum continuous use temperature.
Polylactic acid can be processed like most thermoplastics into fiber (for example using conventional melt spinning processes) and film. The melting temperature of PLLA can be increased 40-50 °C and its heat deflection temperature can be increased from approximately 60°C to up to 190 °C by physically blending the polymer with PDLA (poly-D-lactide). PDLA and PLLA form a highly regular stereocomplex with increased crystallinity. The temperature stability is maximised when a 50:50 blend is used, but even at lower concentrations of 3-10% of PDLA, there is still a substantial improvement. In the latter case, PDLA acts as a nucleating agent, thereby increasing the crystallization rate. Biodegradation of PDLA is slower than for PLA due to the higher crystallinity of PDLA. PDLA has the useful property of being optically transparent.
Applications
Stereocomplex blends of PDLA and PLLA have a wide range of applications, such as woven shirts (ironability), microwavable trays, hot-fill applications and even engineering plastics (in this case, the stereocomplex is blended with a rubber-like polymer such as ABS). Such blends also have good form-stability and visual transparency, making them useful for low-end packaging applications. Progress in biotechnology has resulted in the development of commercial production of the D enantiomer form, something that was not possible until recently.PLA is currently used in a number of biomedical applications, such as sutures, stents, dialysis media and drug delivery devices. The total degradation time of PLA is a few years. It is also being evaluated as a material for tissue engineering.
Because it is biodegradable, it can also be employed in the preparation of bioplastic, useful for producing loose-fill packaging, compost bags, food packaging, and disposable tableware. In the form of fibers and non-woven textiles, PLA also has many potential uses, for example as upholstery, disposable garments, awnings, feminine hygiene products, and diapers.
PLA has been used as the hydrophobic block of amphiphilic synthetic block copolymers used to form the vesicle membrane of polymersomes.
PLA is a sustainable alternative to petrochemical-derived products, since the lactides from which it is ultimately produced can be derived from the fermentation of agricultural by-products such as corn starch or other carbohydrate-rich substances like maize, sugar or wheat.
PLA is more expensive than many petroleum-derived commodity plastics, but its price has been falling as production increases. The demand for corn is growing, both due to the use of corn for bioethanol and for corn-dependent commodities, including PLA.
PLA has also been developed in the United Kingdom to serve as sandwich packaging.
PLA has also been used in France to serve as the binder in Isonat Nat’isol, a hemp fiber building insulation.
PLA is used for biodegradable and compostable disposable cups for cold beverages, the lining in cups for hot beverages, deli containers and clamshells for food packaging.
The pharmaceutical industry uses oligolactic acid (OLA - a shorter polymer of lactic acid) in pressurized metered dose inhalers (pMDIs) as a surfactant. Studies have shown that on standing, pMDIs without OLA will yield a much higher dose than intended as compared to those containing OLA which delivers a fairly constant dosage
Production
As of Jun 2010, NatureWorks was the primary producer of PLA (bioplastic) in the United States.Other companies involved in PLA manufacturing are PURAC Biomaterials (The Netherlands) and several Chinese manufacturers. The primary producer of PDLLA is PURAC, a wholly owned subsidiary of [CSM] located in the Netherlands.
Galactic and Total Petrochemicals operate a joint-venture, Futerro, that is developing a second generation of polylactic acid product. This project includes the building of a PLA pilot plant of 1500 tonnes/year in Belgium.
The Korean research center KAIST has announced that they have found a way to produce PLA using bio-engineered Escherichia coli.
Since 2009, Purac has developed a unique business model by starting production of Lactides (D and L, the monomers for PLA production, in their Spanish production plant with a capacity of several thousands of tons, while in March 2010 the construction has started of a 75.000 tons lactide plant at their production site in Thailand (Rayong Province). Purac has developed the technology to polymerize these lactides with Sulzer, a Swiss Engineering company. Purac collaborates with various PLA production partners to develop production scale and new markets for PLA. Thanks to the availability of D-lactide, Purac partners will be able to use stereo-complex technologies to produce new PLA grades with heat-stability (HDT) up to 180 degrees C, enabling use in higher value application area's. In a tripartite collaboration between Purac, Sulzer and Synbra solutions were developed to allow Synbra to start production of PLA and subsequently E-PLA, an attractive biodegradable and/or biobased alternative to EPS-foam in avariety of application areas. This collaboration was awarded by Frost and Sullivan with the Innovation of the Year Award in 2008 citing "This unique offering will significantly reduce the process and product development time enabling faster and more reliable market entry for PLA producers".
PLA Recycling
In Belgium, Galactic started the first pilot unit to chemically recycle PLA (Loopla). Unlike mechanical recycling, waste material can hold various contaminants. Through thermal depolymerization, a highly purified lactic acid is extracted and can be considered as raw material for the manufacturing of virgin PLA with no loss of original properties (cradle-to-cradle recycling).
procedure
Polylactic acid is a synthetic dermal filler that is injected into your face, causing your body's own production of collagen. This type of dermal filler is known as a stimulator. This non-toxic, biodegradable substance has been used for more than 40 years as suture material. It's known to work particularly well in the lower half of your face, to fill the lines caused by laughing, to augment thin lips and fill out deep nasolabial folds. This substance is unlike other dermal fillers because it doesn't produce immediate results. Instead, it stimulates your own body's collagen production, so results appear gradually over a period of a few months.Prior to injection, your plastic surgeon will add sterile water to reconstitute the polylactic acid. Then it's injected into the deep dermis or subcutaneous space with a special technique called tunneling or threading. It is important to distribute polylactic acid evenly to minimize the possibility of inflammatory formations called granulomas.
You will likely need about three monthly treatments to achieve your desired results. With each treatment, there is re-stimulation of your own collagen. Then it can take four to six weeks to see the full effect. While this type of dermal filler is considered semi-permanent, you may still need occasional touch-ups.
The only FDA-approved brand is Sculptra Aesthetic.
Choose a qualified plastic surgeon
Polylactic Acid injections are sometimes performed with no medical oversight, often in conjunction with facial spa treatments. You can avoid any risks or complications and achieve optimal results by visiting a qualified plastic surgeon. Although the surgeon may not perform the procedure, you can rest assured that the surgeon's employees are properly trained and supervised.Visit the online referral service of the American Society of Plastic Surgeons (ASPS). ASPS, founded in 1931, is the largest plastic surgery organization in the world and the foremost authority on cosmetic and reconstructive plastic surgery. All ASPS physician members are certified by the American Board of Plastic Surgery (ABPS) or the Royal College of Physicians and Surgeons of Canada.
0 comments:
Post a Comment